The mantra of 2020 has been “it’s time to build” and Cover is a company doing just that — literally. Today Cover, a full-stack homebuilder, is announcing that Founders Fund is leading their Series A, along with participation from Lennar, Valor Equity Partners, General Catalyst, 50 Years VC, and Khosla Ventures. Capital-intensive businesses eh?
Before we dive into what Cover is working on, it’s worth taking a step back and talking about the history of home building, and what some of the more recent innovations in the space have been. One of the first major innovations in homebuilding was in 1832, when “balloon framing” was introduced which allowed for much easier and less wood-intensive multi-level home construction. Below is a photo from a home being built in 1877 in Nebraska with this technique.
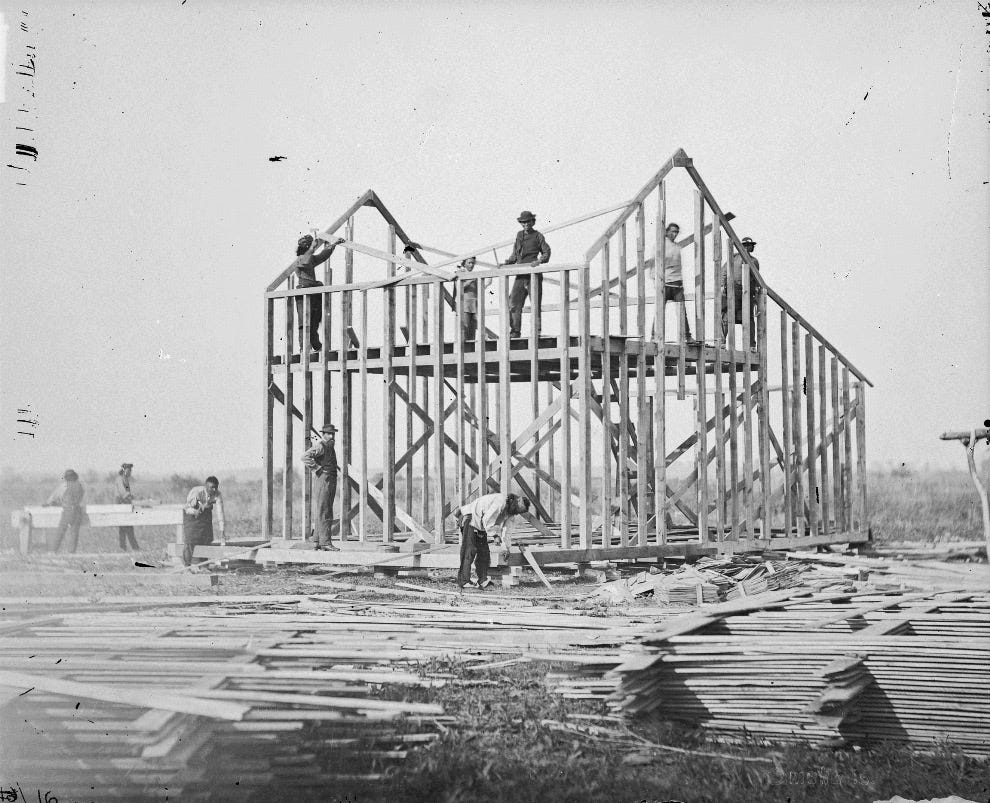
Unfortunately, one would have hoped that 190 years later the process of homebuilding would have radically changed and simplified. Instead, it has only gotten more complex, as at the turn of the 20th century, amenities such as heating and plumbing became much more common. Homebuilding now required several different types of skilled labor that needed to be coordinated rather than mostly woodworking. This introduced a ton of cost and logistical challenges as now, the woodworking had to take into account pipes and ducting that had to run through the interior cavities of the home. If there were mistakes in this preparation, which was common, the easiest way to fix it was to bring in the skilled plumber and have them reshape the pipes into whatever shape would work with the current version of the structure.
A popular saying at that time was, “When building a home, there are 3 major factors. Quality, Cost, and Timeline. You can pick 2 of them to control”. No matter what, when building a home you had to make trade-offs.
Innovation in Home Construction before Cover
The traditional homebuilding process essentially looks like the following: ship a bunch of construction materials to a site, hire a bunch of skilled labor to assemble it, roughly following a schematic but mostly just working off their instinct and eyeballing it. In the more recent years there have been some attempts at innovating on this process, although, I believe they have all fallen short.
The first major innovation was called “prefabricated homes”. The idea is you’d build most of the home inside of a factory rather than building homes on-site, where you are subject to weather delays, and relocation of your building crew/long commutes. There are a couple of problems with this approach. First, you’re still building homes the same ol’ way, i.e. skilled laborers like plumbers & electricians working manually on custom projects. Second, in the prior model you can “flat-pack” all your construction materials onto a few trucks and ship them over to the site. With prefab, you instead have to ship over a whole home, which takes up many more trucks since you can’t flat-pack it, and then once it arrives, you need to crane it into position. As it turns out, most of the economic gain that you get from having your employees commute to a single location and not having to deal with weather delays, gets lost from all the additional cost of installation.
Ok, so back to the drawing board! How do we make a home in a factory, but not deal with the cost of shipping an entire home? Well the next step of innovation was called “modular housing”. What that meant was you still used high skill labor, but now rather than building an entire home in the factory, you would split it up into pieces, building a whole wall, or ceiling with all the electrical + plumbing. That way, you can flat-pack it all and you don’t have to crane in a home, instead you would just put together the lego pieces. The problem with this approach has been that plumbers, electricians etc. aren’t working with extremely tight tolerances during their building process in the factory. So when all the pieces arrive on-site, if you have a couple of ceiling “modular pieces”that are a bit too long, your ceiling ends up hanging off the side of your building. Turns out you end up having to send in highly skilled labor to touch up all of these assembly issues, and so this whole process ends up, yet again, not being much better than just having done the traditional homebuilding process from the get-go.
So, unfortunately, despite being the major cost item in most people’s lives, the economics of building and owning and renting a house remains largely unchanged from where it was 190 years ago, unlike almost every other line item (aside from healthcare and education), which has massively decreased in real dollars. So how do we do the same with homes? How do we massively decrease the cost structure? Well we need to pull out the need for highly specialized labor and instead make this a highly repeatable and efficient process which can be done by less skilled labor.
Well where has this done before? With cars of course! In 1913 Henry Ford invented the moving assembly line which massively decreased the cost of producing a car and opened up car ownership to the masses.
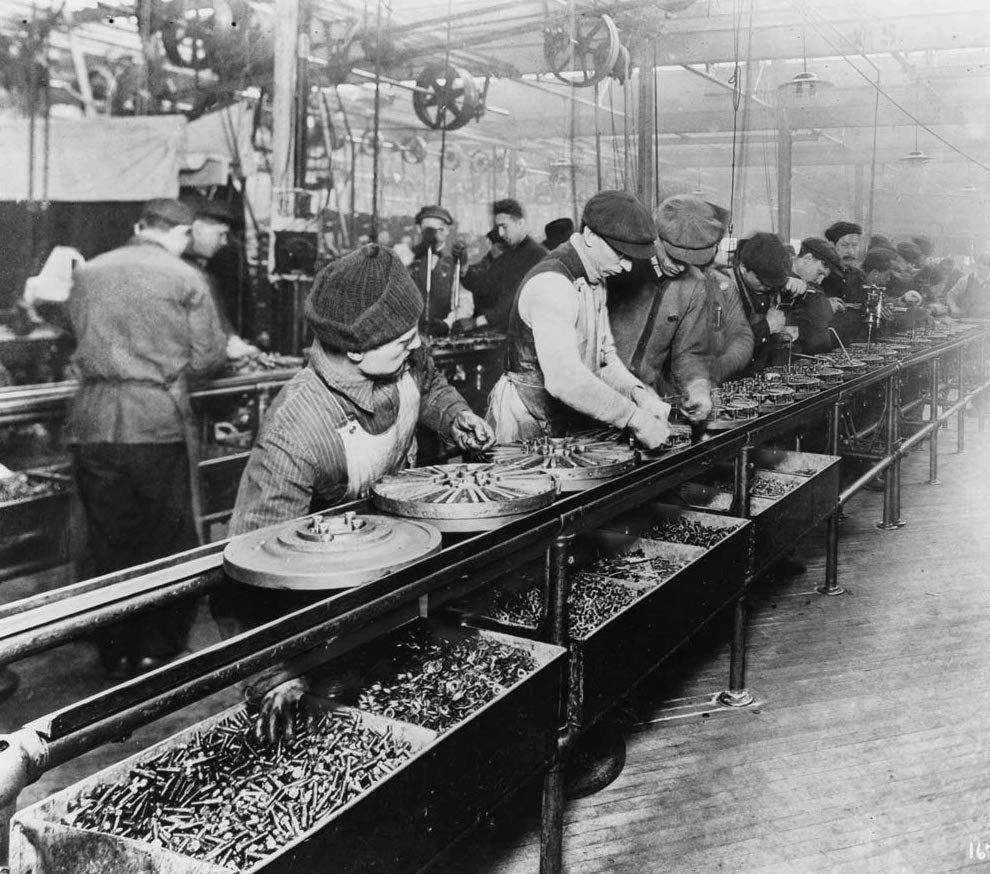
Cover
So, what does Cover do? Cover is a full-stack home-builder, starting off with a market focus on additional dwelling units (ADUs) in the LA area. That means that customers can come to Cover with some space in their backyard and Cover will handle everything from design, architecture, permitting, foundation & sitework, construction, appliances, and all the way to a certificate of occupancy. Most of the startups going after this space tend to just be marketing landing pages + some design software, and then they hand off the construction to a traditional property developer or general contractor. Which doesn’t really innovate on the core cost structure…
Cover produces homes like this (link):
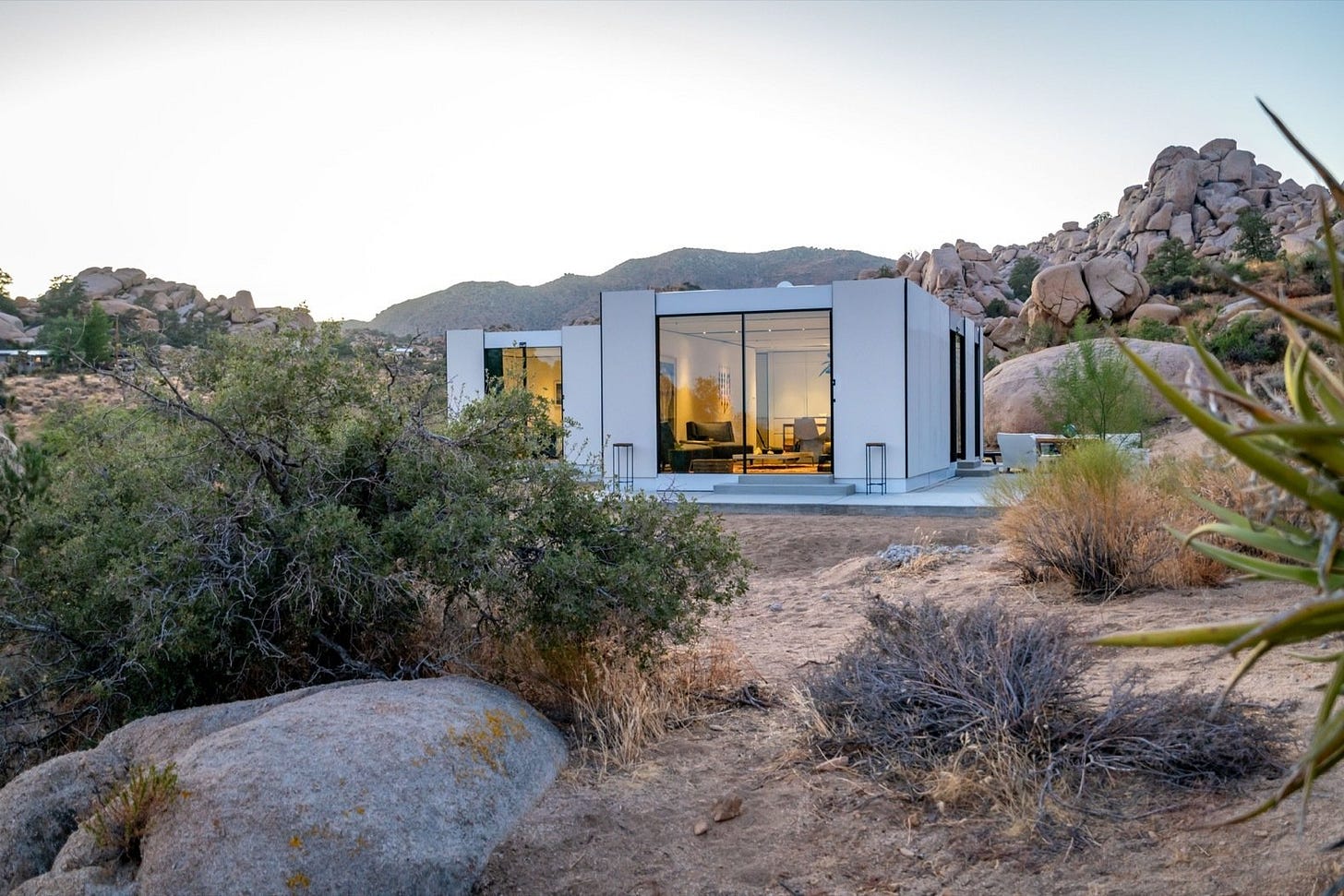
And like this (link):
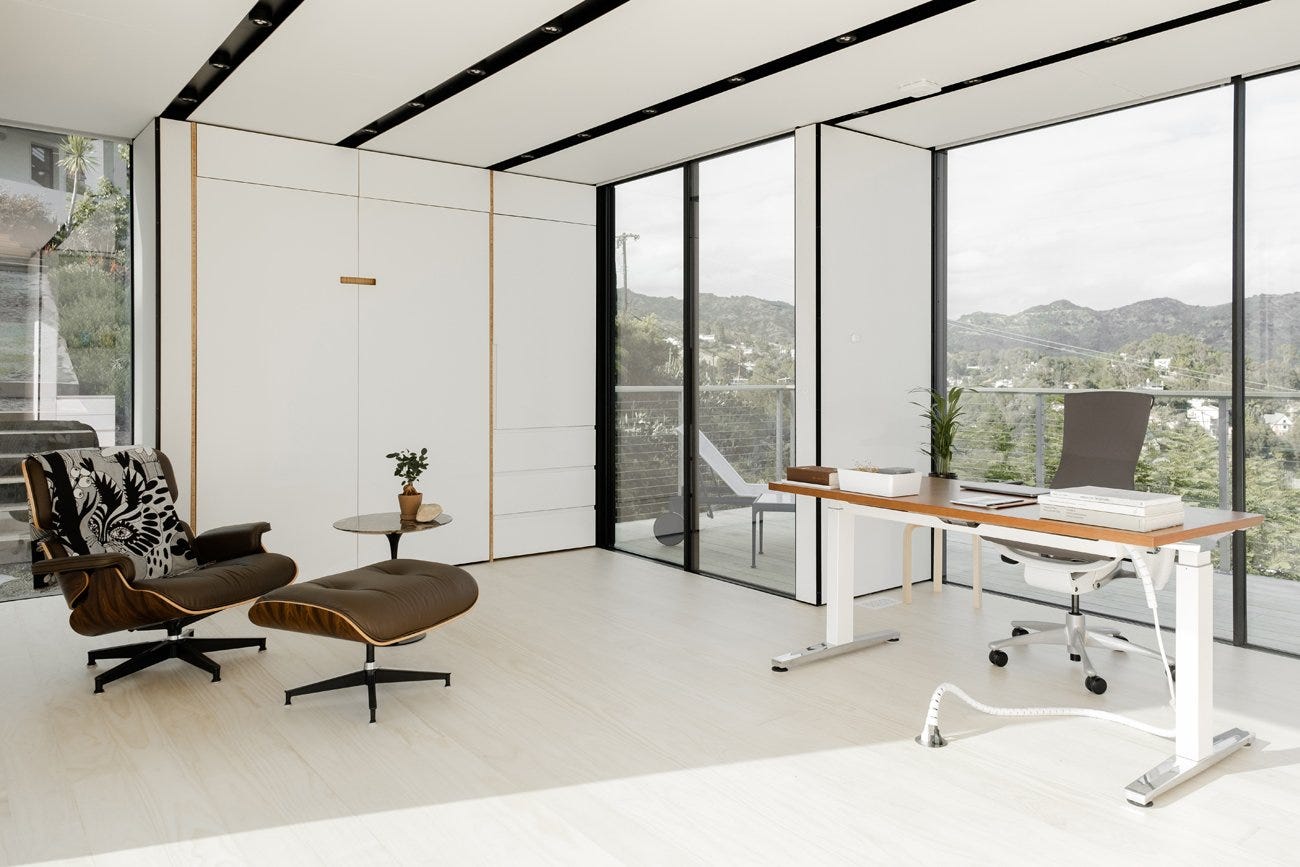
But these homes are all made of modules, made on an assembly line, in a factory, by low skill labor + automation, at aerospace-levels of tolerances, meaning that when we take those modules to a site, they fit together perfectly. This cuts out the biggest cost component, the skilled labor like plumbers, electricians etc.
And, most importantly, unlike any other company that has tried to create the “assembly line for homebuilding,” each of their homes is a completely custom design. No cookie-cutter homes here. It involves a lot of complicated software and mechanical engineering, but Cover lets you design your perfect home, which then gets chunked down into modules, assembled on their line, shipped to your site, and assembled in just a few weeks.
Cover is the future of homebuilding, with zero compromises, fully customizable, high quality, and on our way to being cheap and available to the masses as we follow the Tesla approach of Roadster → Model S → Model 3. Come and join us on this journey by visiting their website, (link). It’s time to build.
P.S. Feel free to check out their Forbes coverage today (link) and a podcast Solana and Alexis (CEO of Cover) did to discuss the future of housing (link)